Intumescent coating types
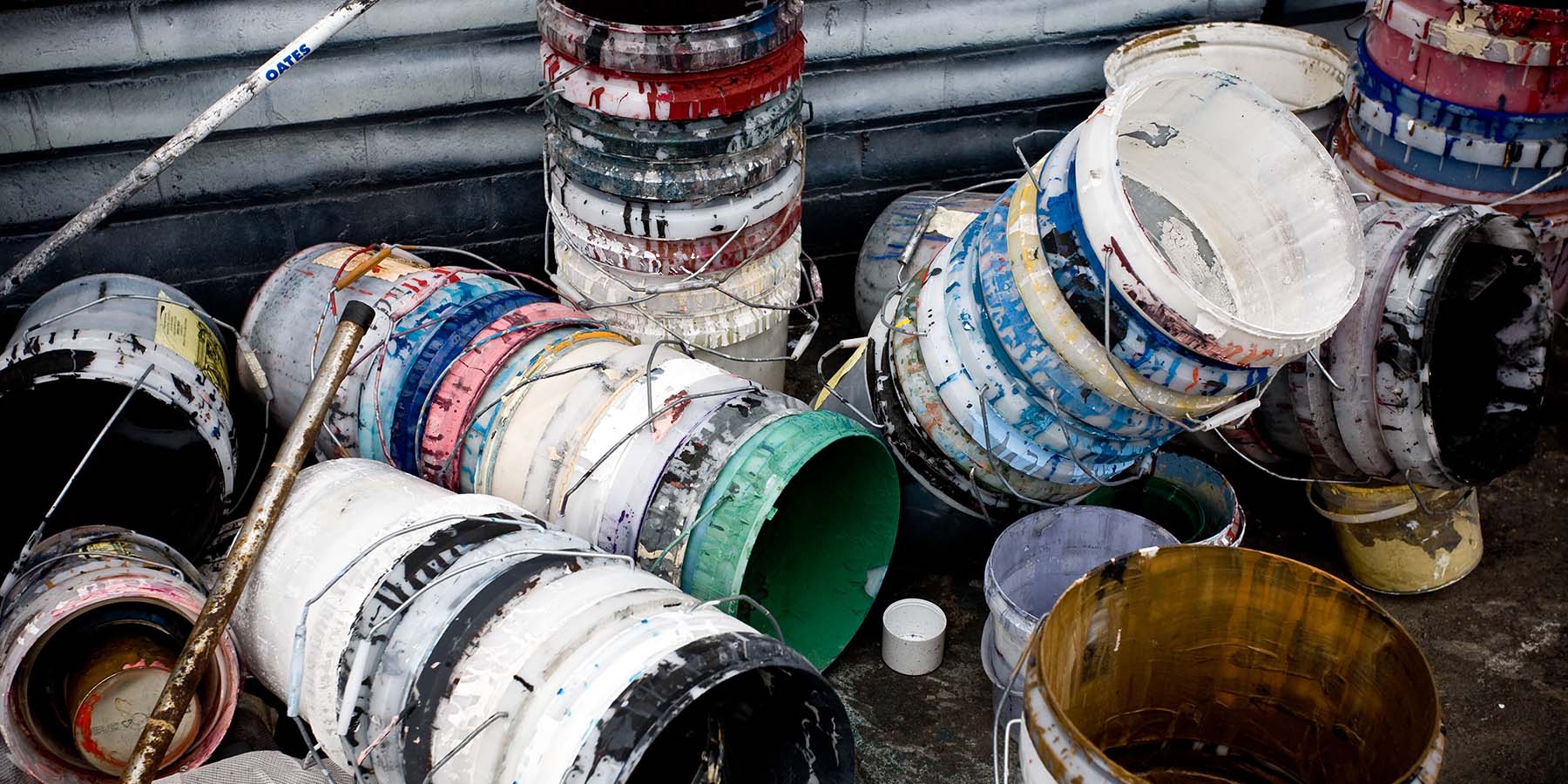
Intumescent is the newest fire protection methodology to come onto the market. Unlike boards and vermiculite, intumescent is a reactive material which expands to insulate structural steel in a fire event. Every intumescent has different material properties and therefore have different required thicknesses and expansion behaviour.
Solvent-based systems
Solvent-based coatings usually used in semi-exposed environments and are tested against weather and temperature variations. Solvent-based coatings tend to be more resistant to weather conditions as well as temperature changes and humidity. They also dry faster and have a smoother finish.
Advantages
- Suitable for internal steel or semi-exposed and exposed steel work when top sealed
- Can be applied off-site or on-site
- Relatively hard film when fully cured
Disadvantages
- If applied on-site it can be damaged by water if not fully cured
- Has high VOCs which can be an OH&S issue if applied on-site
- Requires multiple applications to achieve higher film builds
- Curing could take between 5 and 15 days depending on ambient conditions and film build
Example products
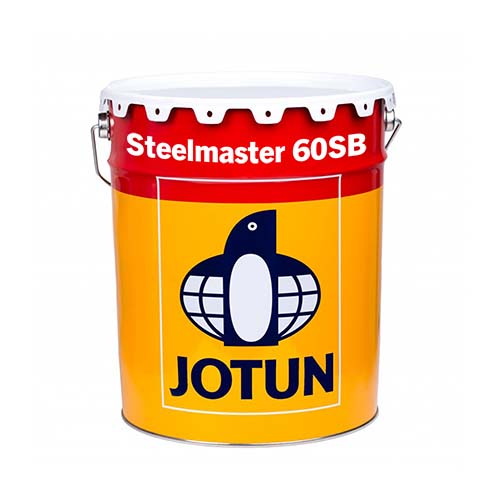
Water-based systems
Water-based intumescent coatings are a generally more eco-friendly and less "chemically-smelling" option. They are the least expensive and produce less odour, however these coatings are less tolerant to humidity and low temperatures and therefore may take longer to completely cure in such environments.
Advantages
- Very Low VOC
- Low odour so does not impact on other trades when applied on-site
- Can be applied to a smooth finish
- Relatively simple to repair
Disadvantages
- Can only be applied on-site in fully protected areas
- Very sensitive to high humidity or moisture
- Requires multiple applications to achieve higher film builds
- Curing could take between 5 and 15 days depending on ambient conditions and film build
- Can be prone to damage easily
Example products
Epoxy-based systems
Epoxy-based intumescent is typically used in harsher environments such as the offshore marine industries or the chemical industry because these coatings provide excellent hydrocarbon fire protection. Epoxy-based intumescent comes in two-parts which when combined, forms a very thick and durable film that insulates the steel member and is highly resistant to corrosion.
Advantages
- Low VOC
- Cures to a very hard durable finish
- Suitable for application for both internal and external steel work
- Generally applied off-site
- Relatively resistant to damage when handled or transported
Disadvantages
- Not generally suited to on-site application due to more complex application equipment requirement
- More expensive product in comparison to conventional intumescent coatings
- Higher film builds require multiple applications over several days
- Cured epoxy intumescent although hard can be brittle and be susceptible to impact damage
- Cured epoxy intumescent can crack and delaminate if coated steel deflects
Example products
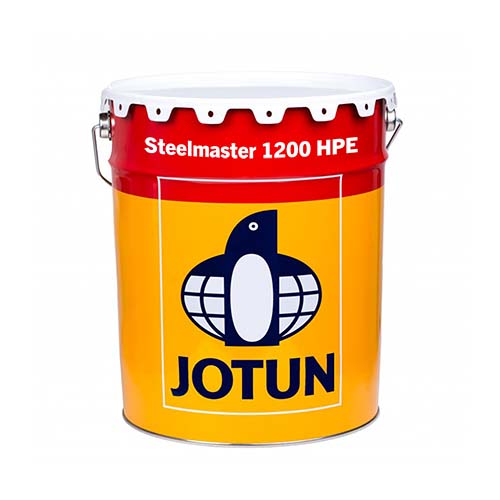
Download the PDF
click hereMore articles...
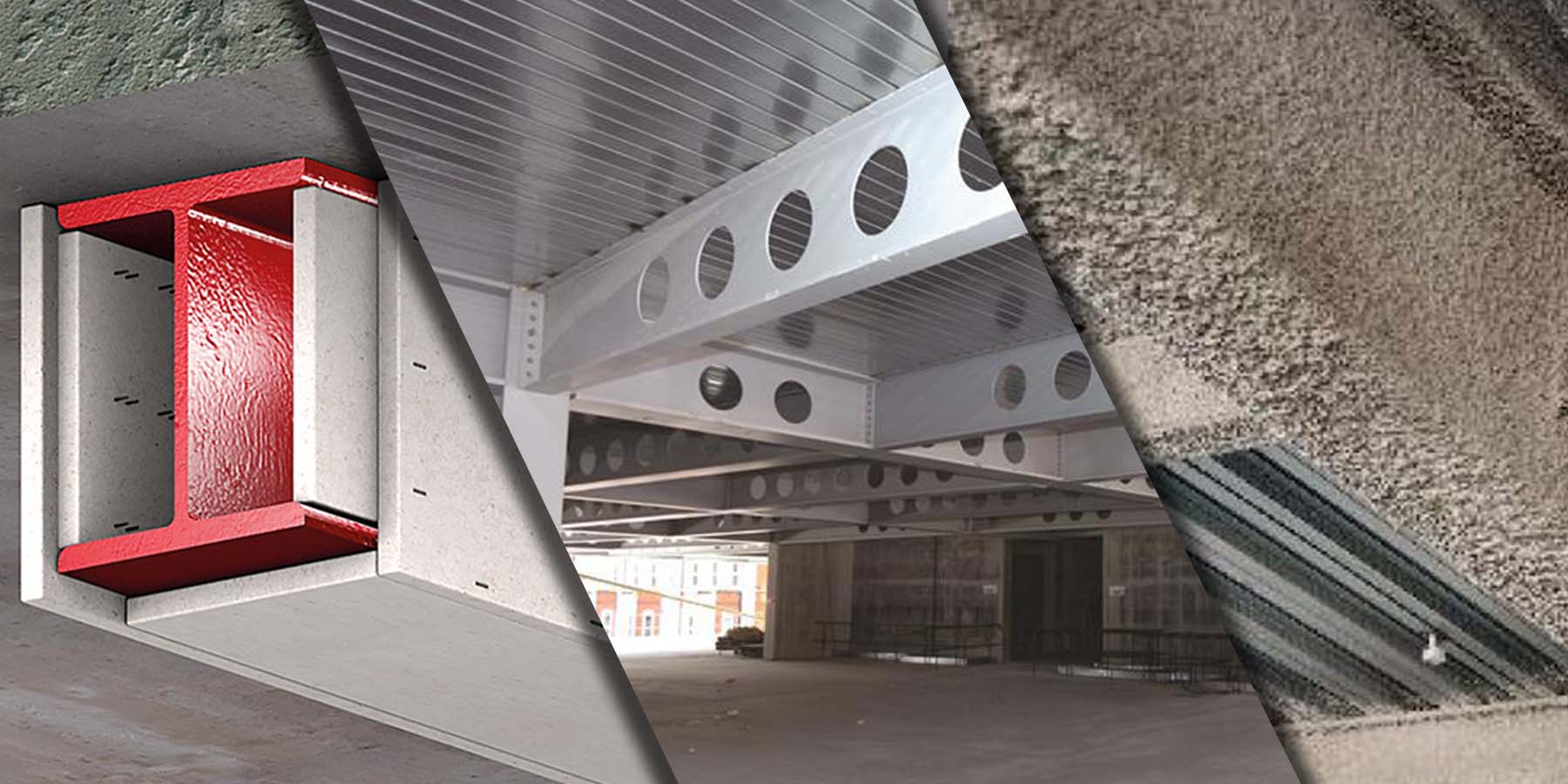
Passive fire protection methods
There are several ways to protect building structural work. Whilst some methods may be more prevalent, there is no one "best way" to protect a building's structure. The best method will most likely be determined by a number of factors, but here are your options.
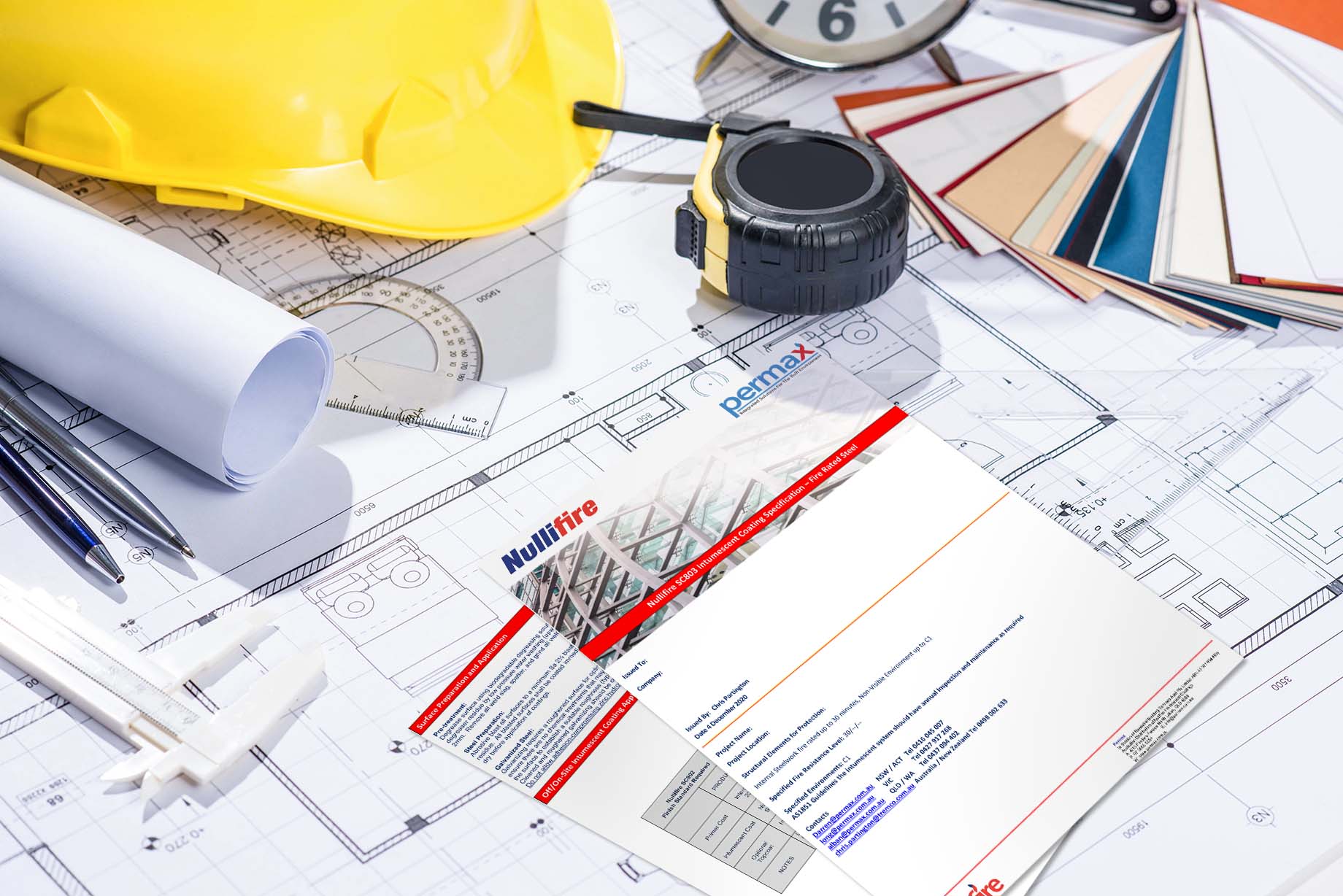
Intumescent paint coating specification templates
Access a range of templates supplied by manufacturers for the purposes of specifying their intumescent paint coating products for various FRLs and corrosivity ratings.
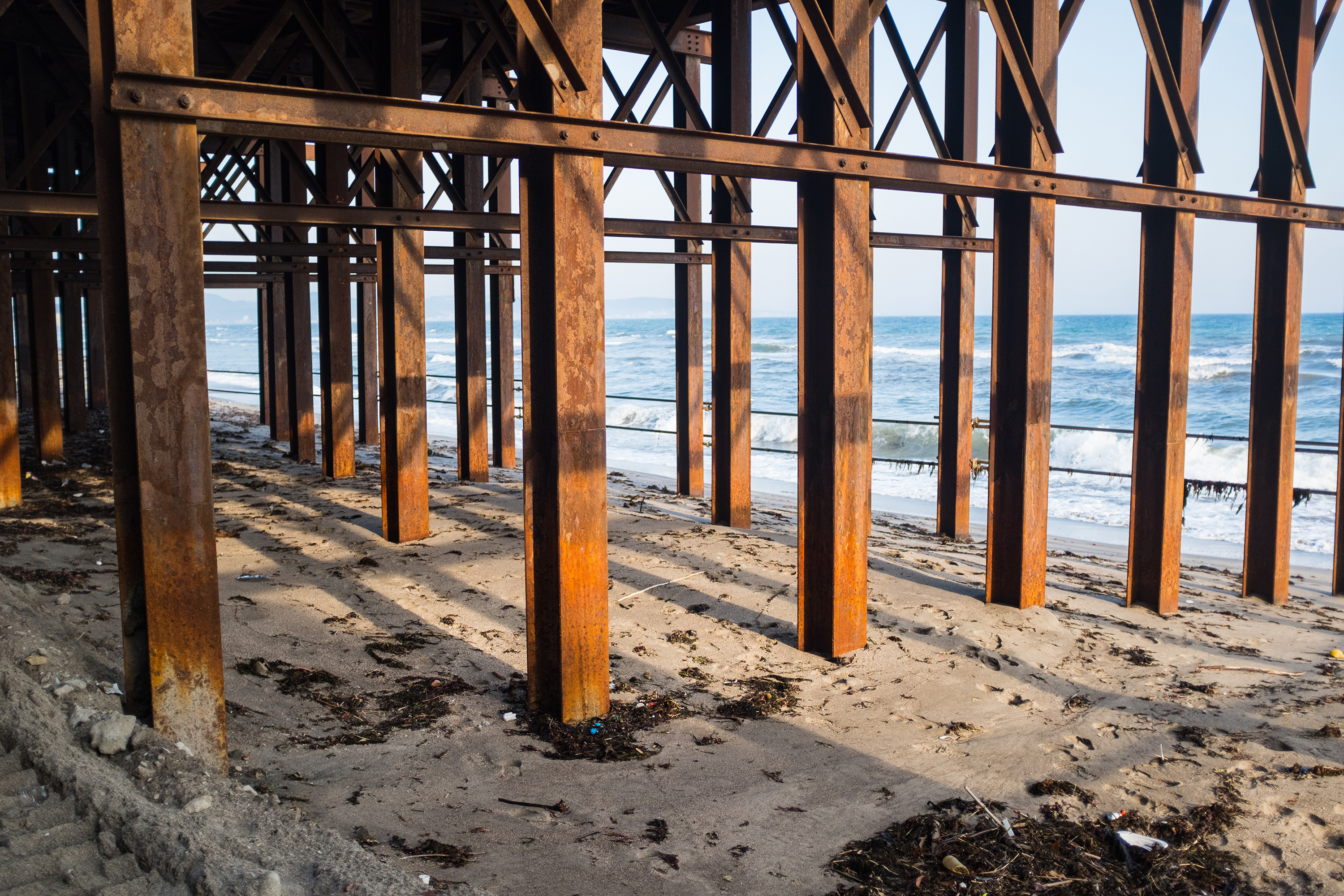
Intumescent paint coating corrosivity ratings in the Australian atmosphere
It's common knowledge that corrosion rates are affected by environmental factors, but do you know the various corrosivity ratings and their definitions?
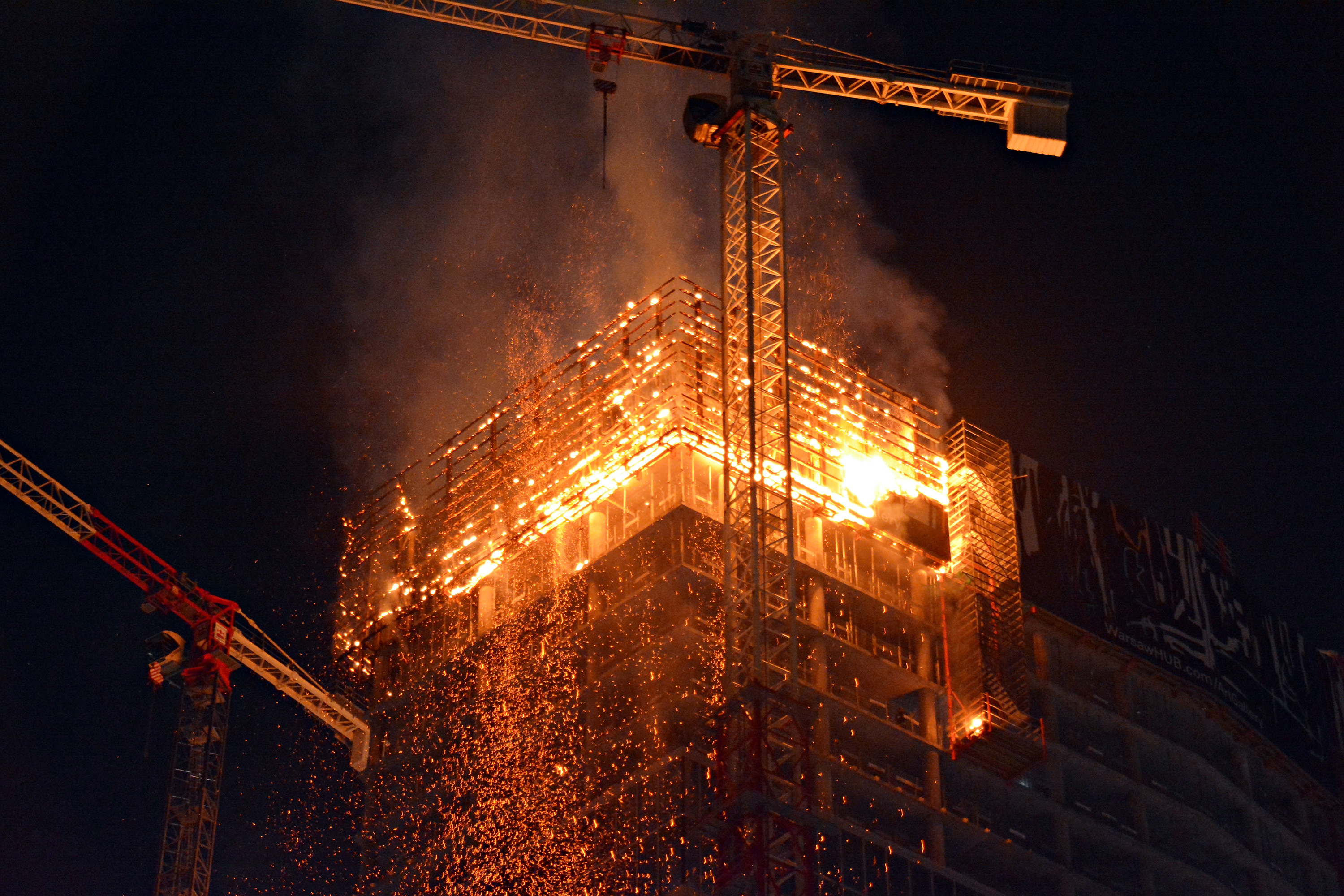
Limiting steel temperatures to maintain structural integrity
Maintaining structural adequacy on load-bearing steel is critical to the fire safety of building occupants, fire fighters and the surrounding built environment. Here's how limiting steel temperatures to maintain structural integrity relates to intumescent paint coatings.
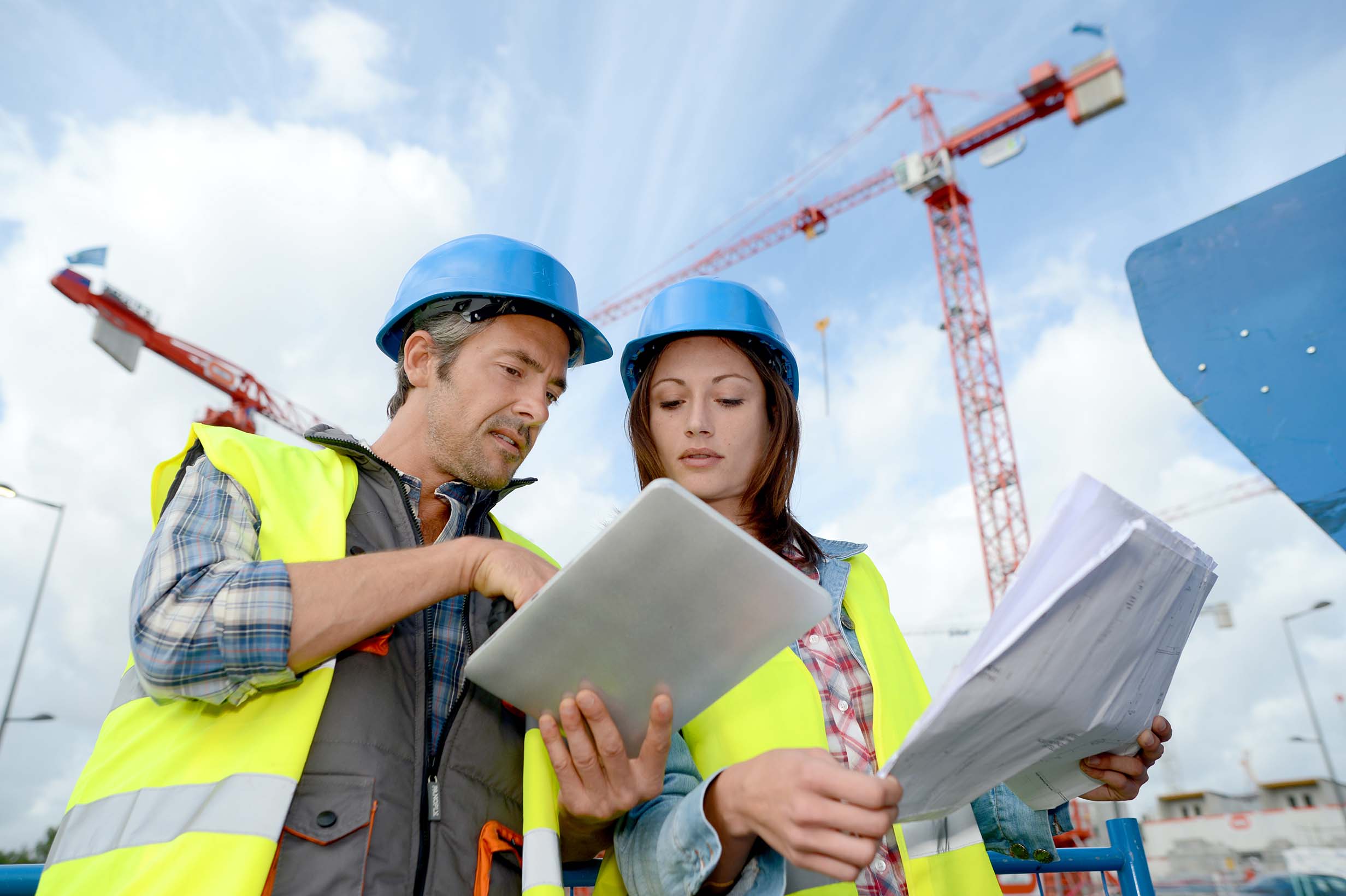
Getting help with intumescent paint coatings
The specifying and application of an intumescent coating system is a highly specialised task that requires considerable training and experience to accomplish correctly.
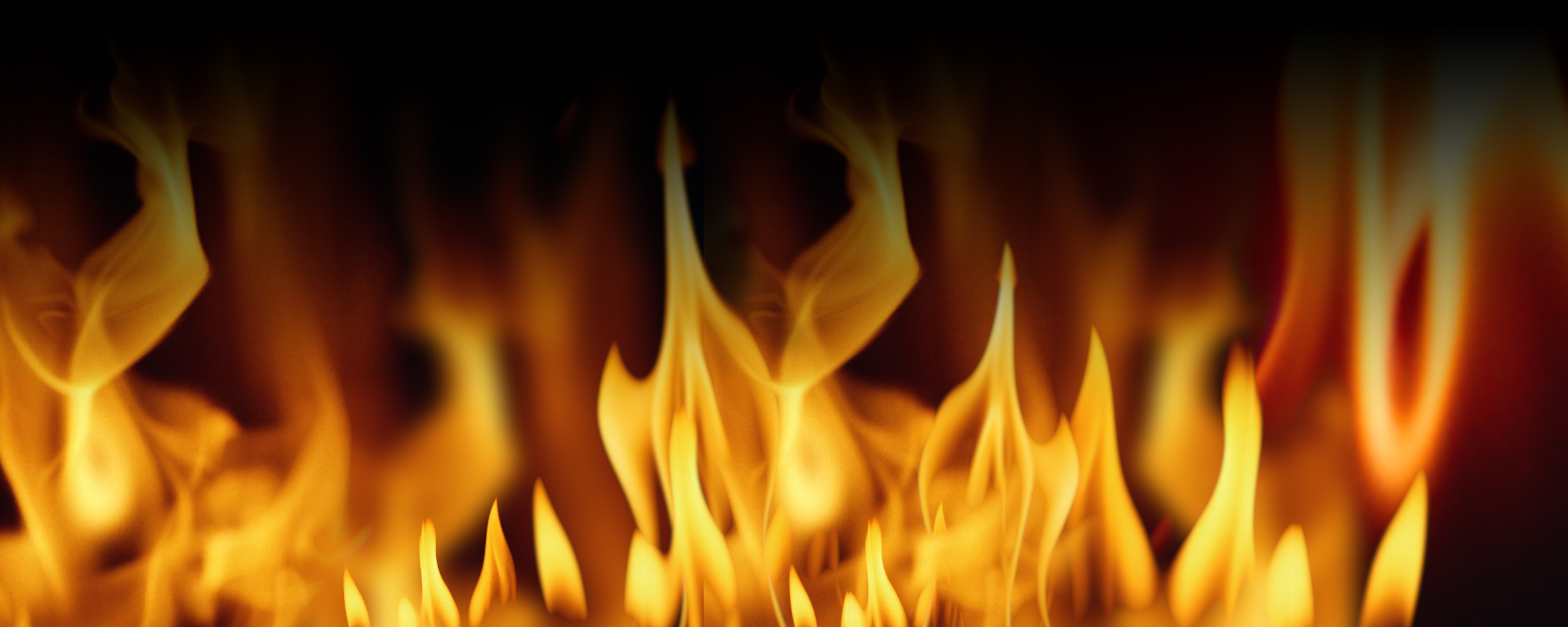
Fire types and severity
Different combustible materials burn at different temperatures which will have a bearing on the FRL of a given intumescent paint coating. This needs to be taken into account when specifying intumescent products so that the required FRL is ensured for the combustible materials that are likely to be encountered in a particular situation.
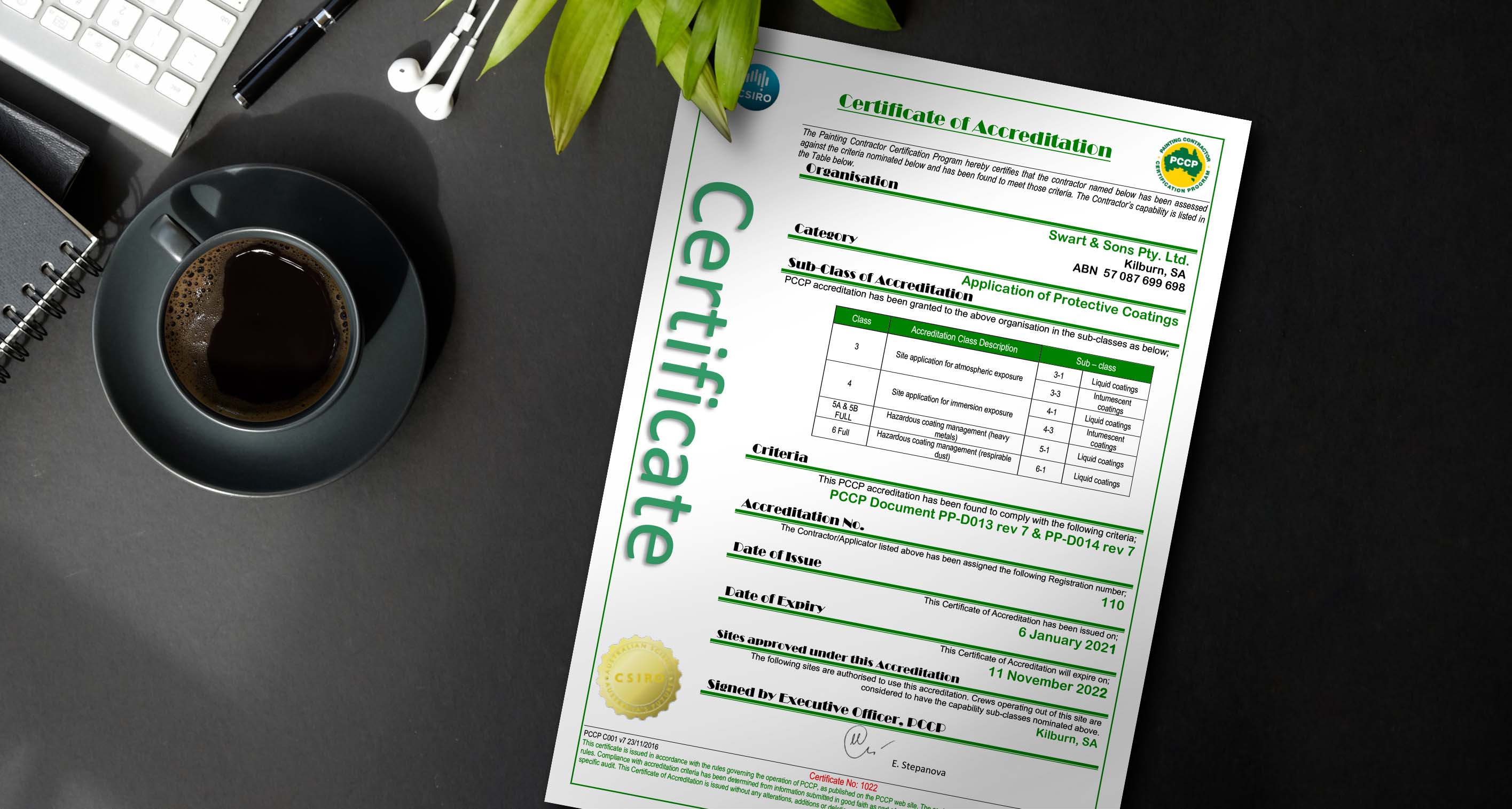
Quality assurance for intumescent paint coatings
We believe Painting Contractor Certification Program (PCCP) accreditation is paramount for passive fire protection contractors engaged in applying intumescent paint coating systems.
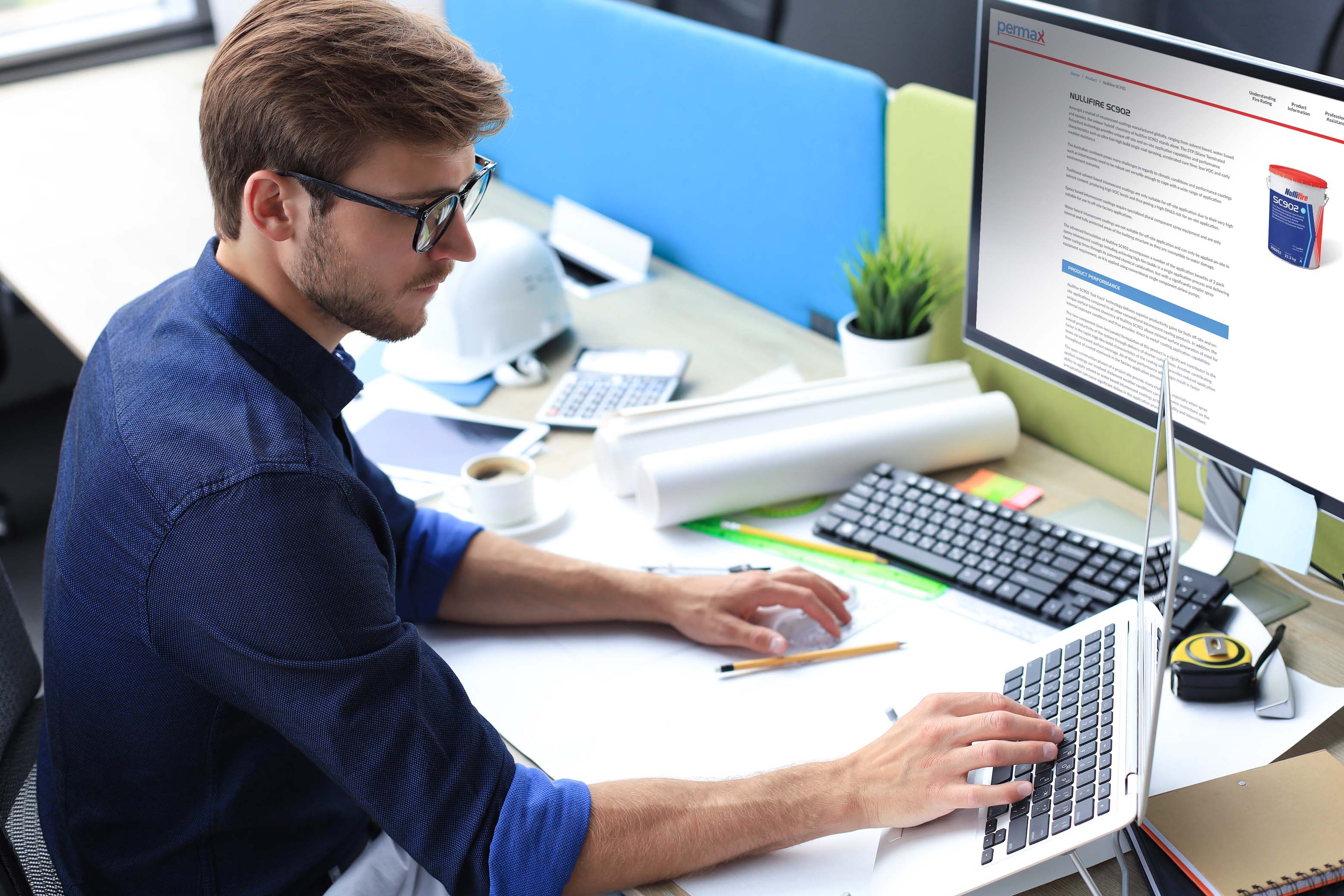
Specifying intumescent paint coatings
Whilst intumescent coating products may look just like paint, they have an important function (i.e. passive fire protection) that makes their specification a much more involved process.
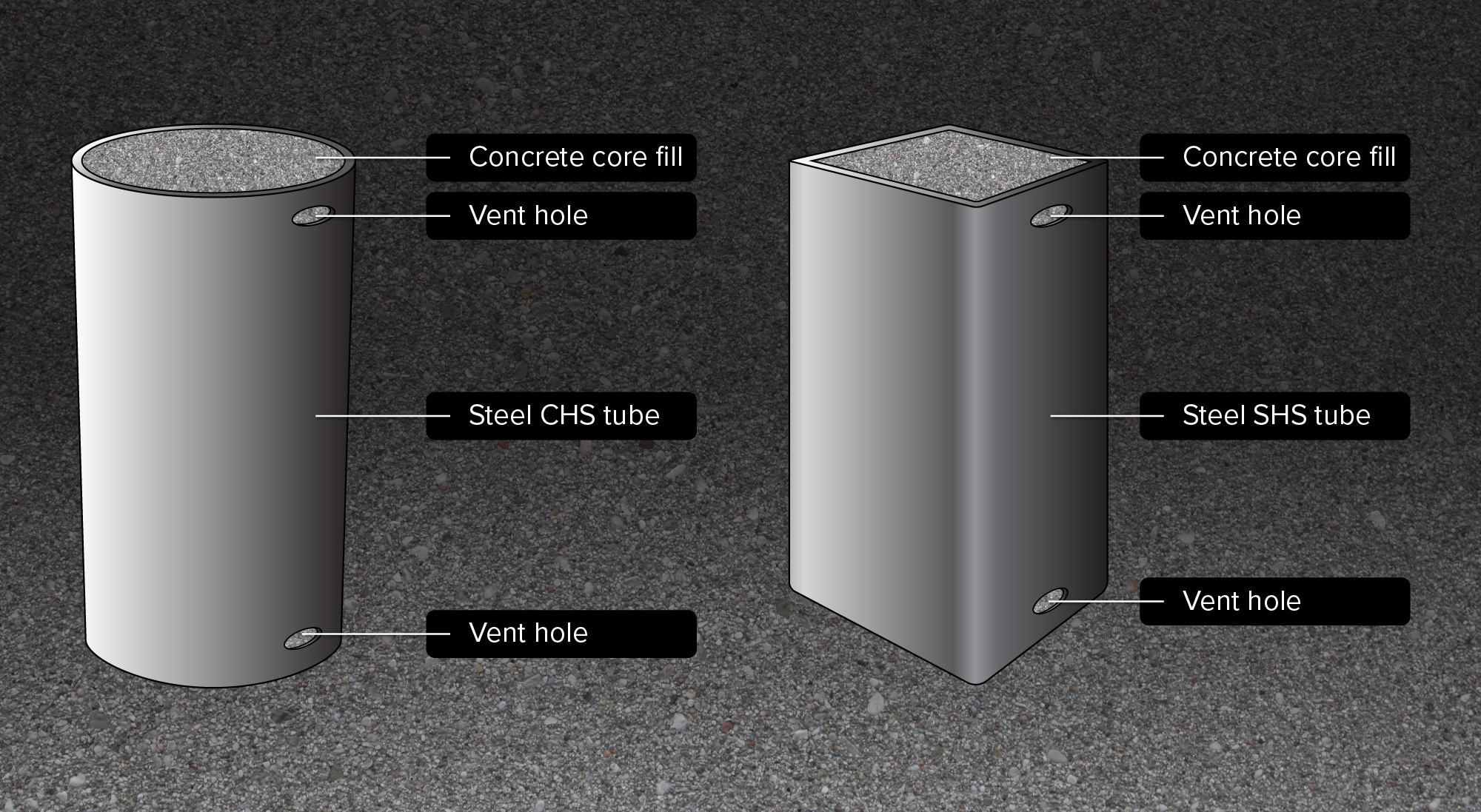
How core filling affects intumescent paint coatings
Core filling is a viable solution to fire-protect high Hp/A hollow section steel that is otherwise unable to achieve the desired FRL.
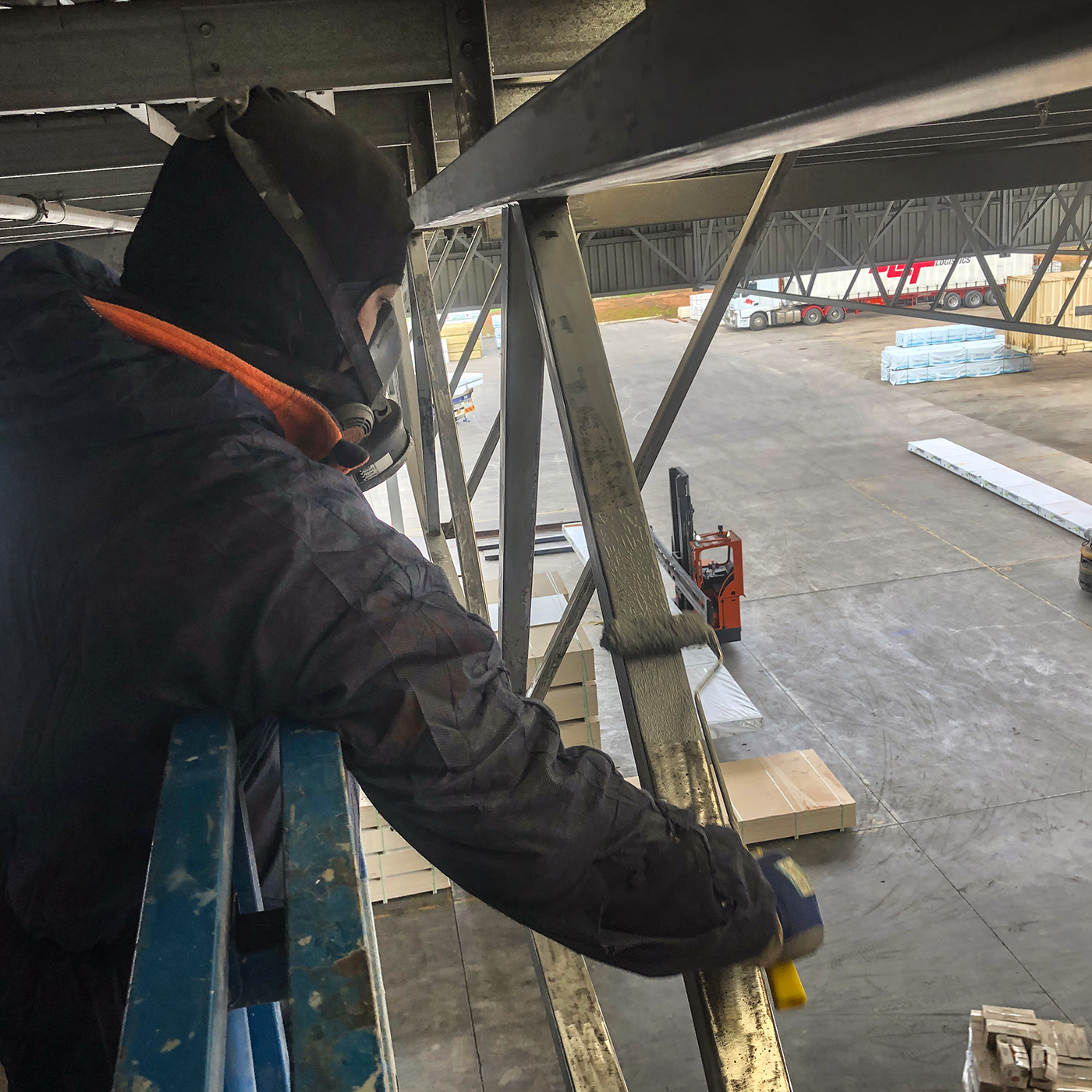
Applying intumescent paint coatings
Builders need to choose appropriately qualified subcontractors that are licensed to do work in the relevant state or territory, i.e. they are licensed to apply intumescent paint coatings.